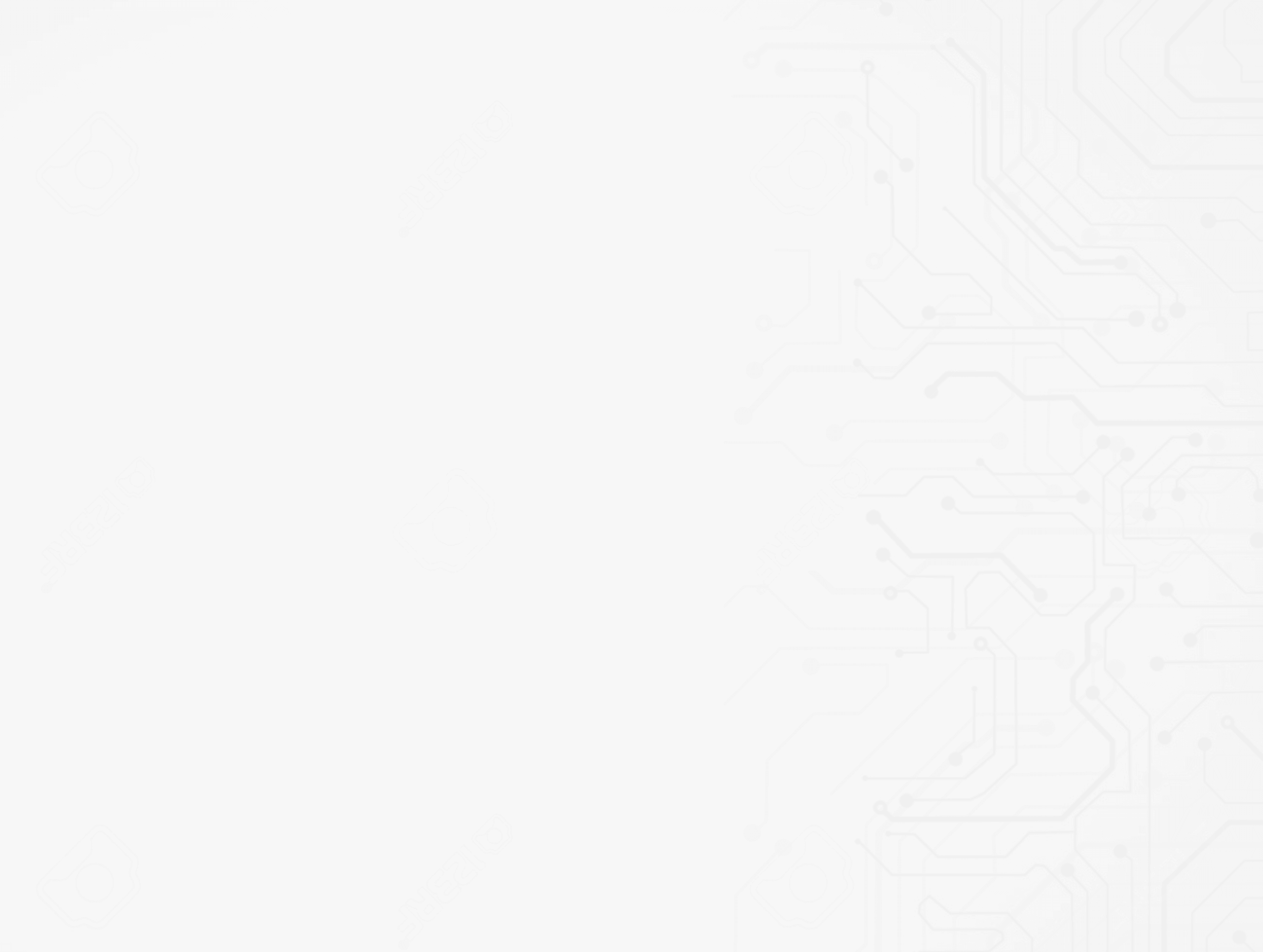
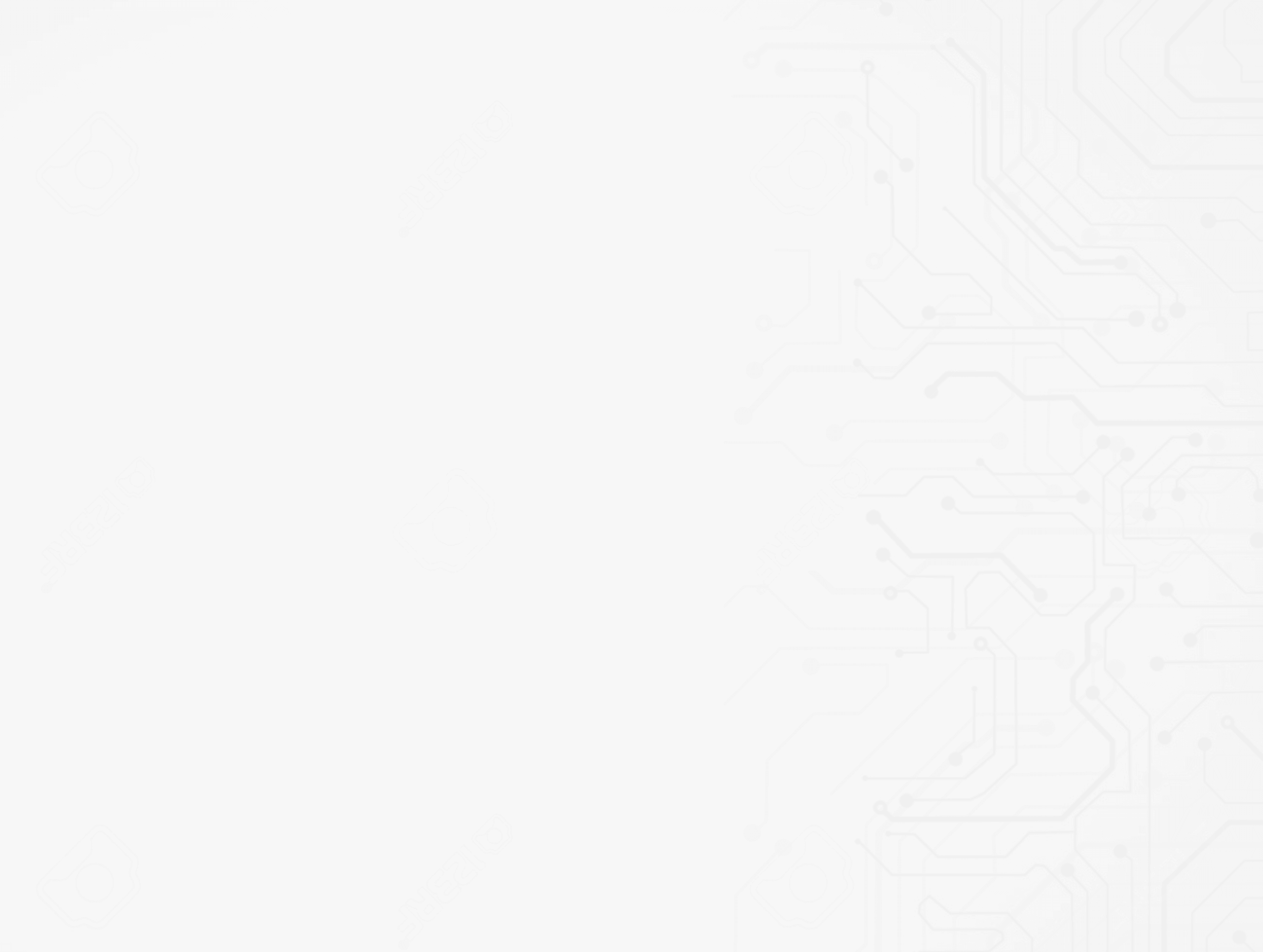
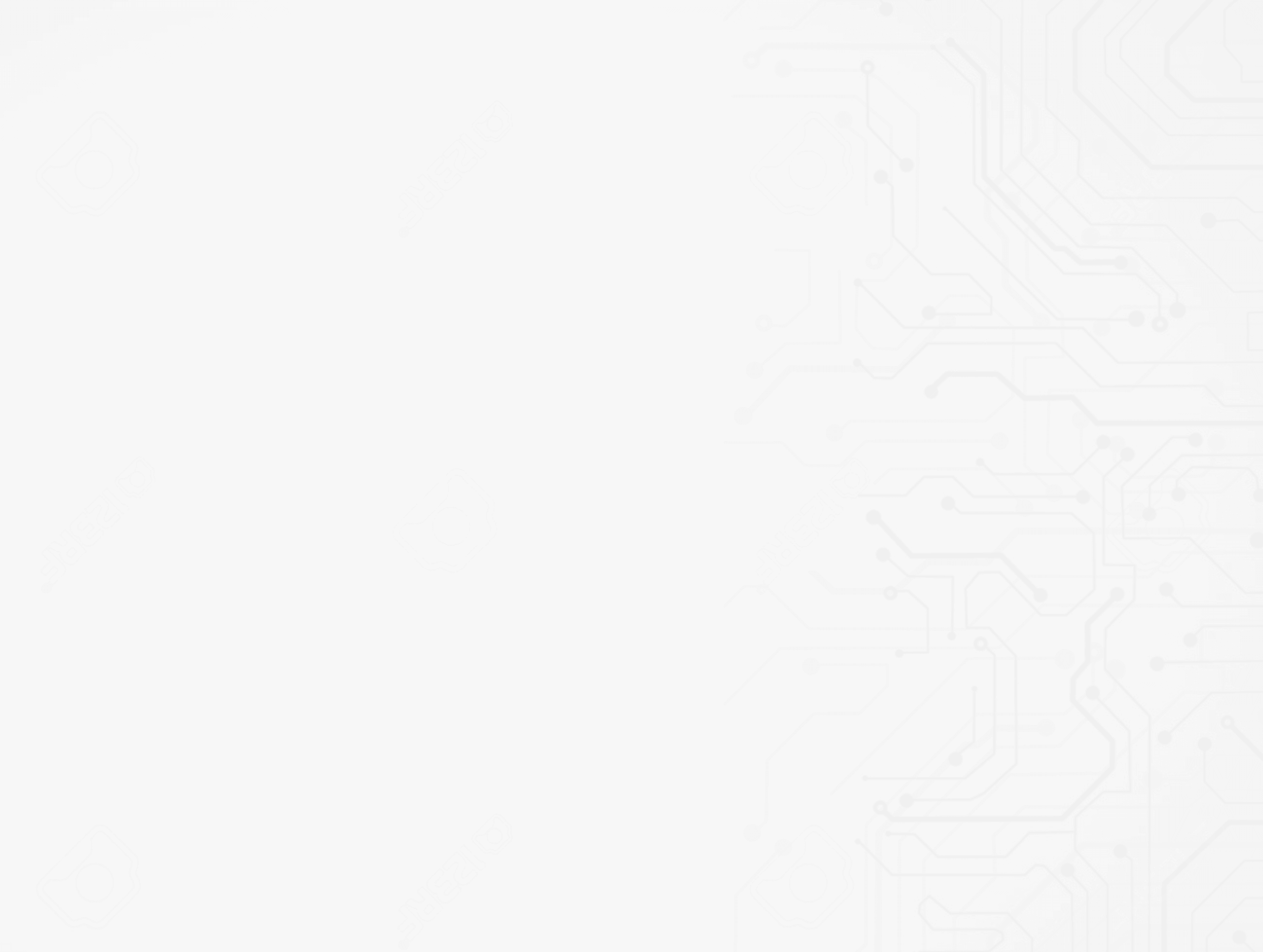
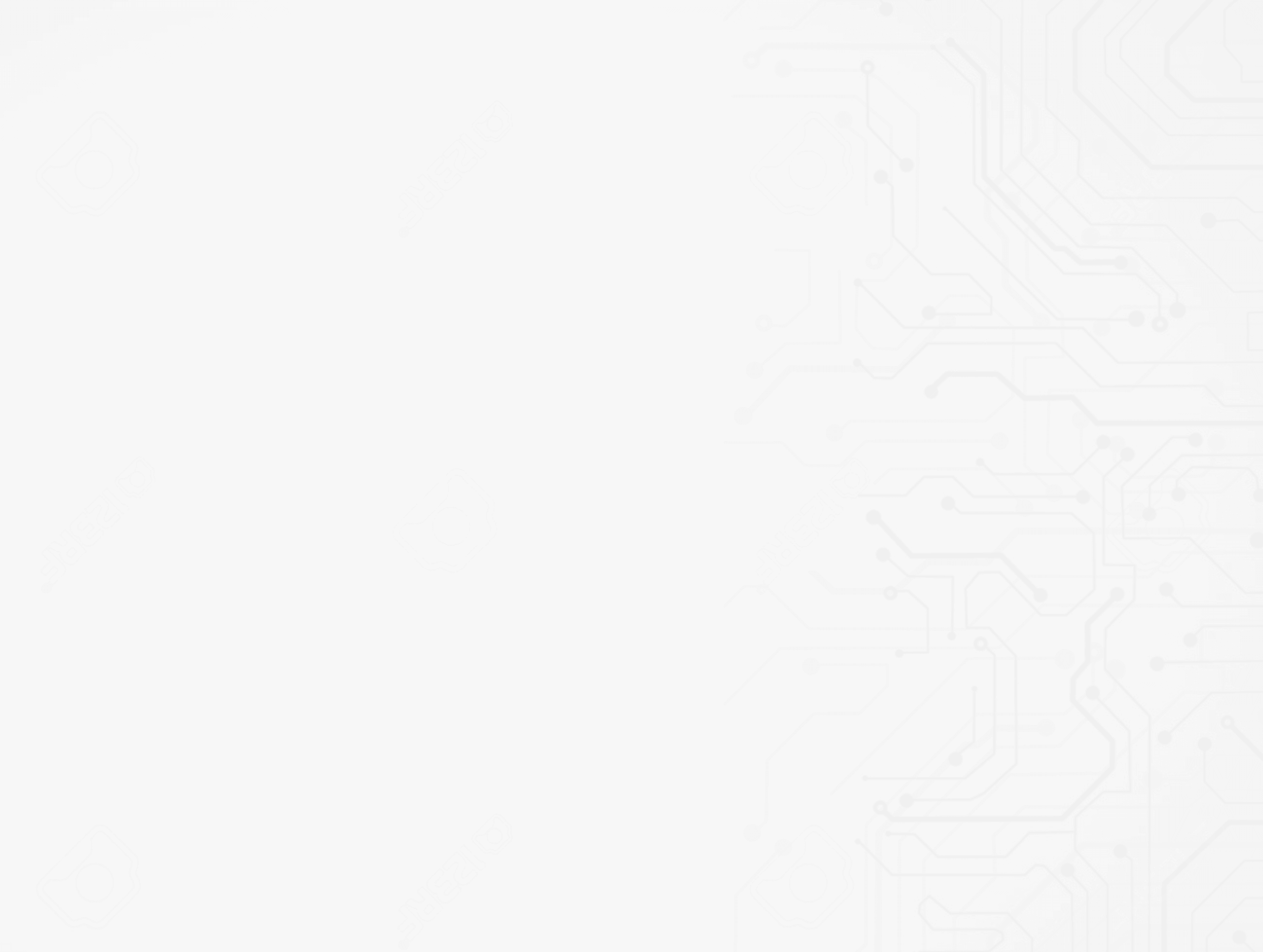
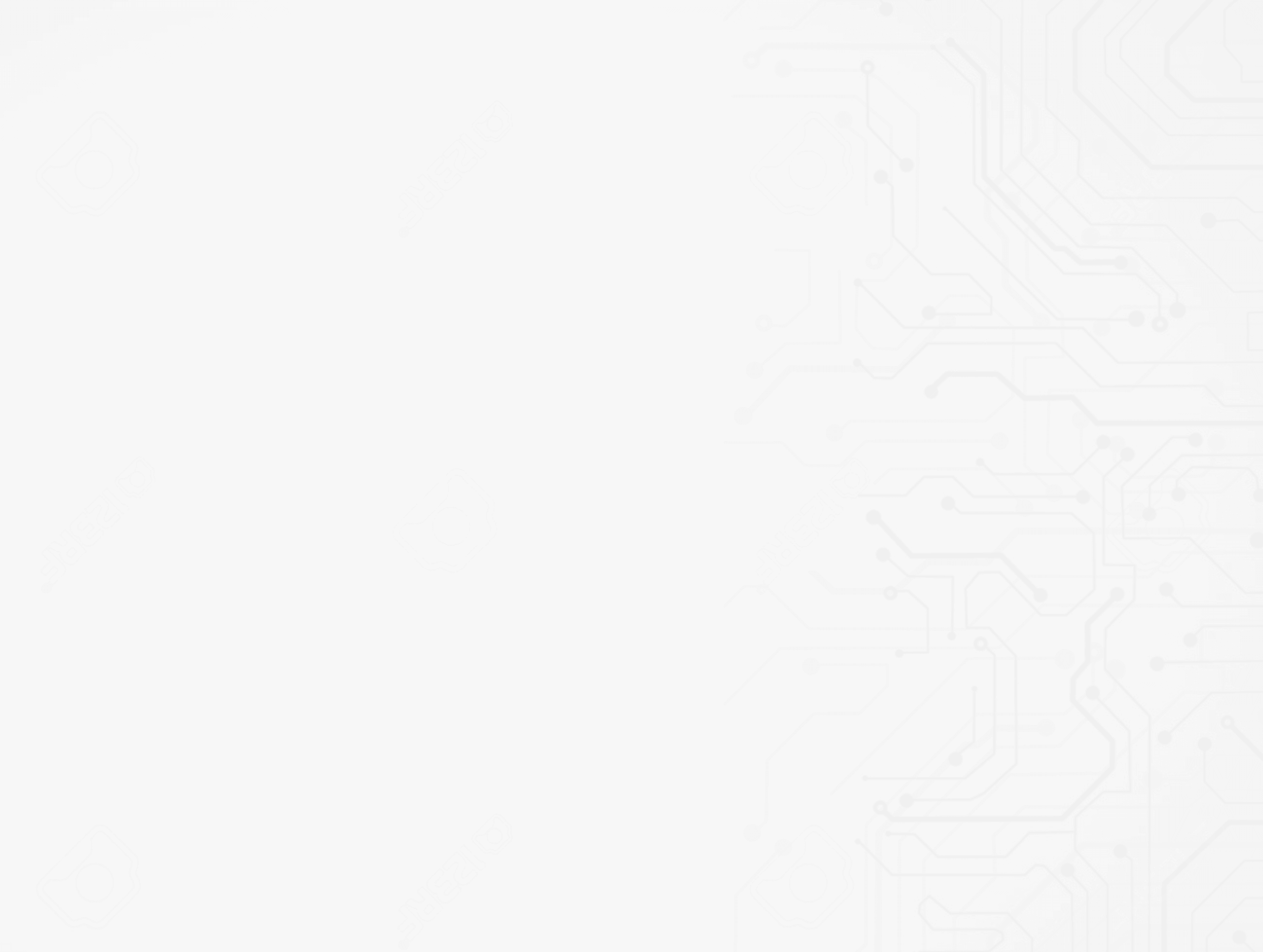
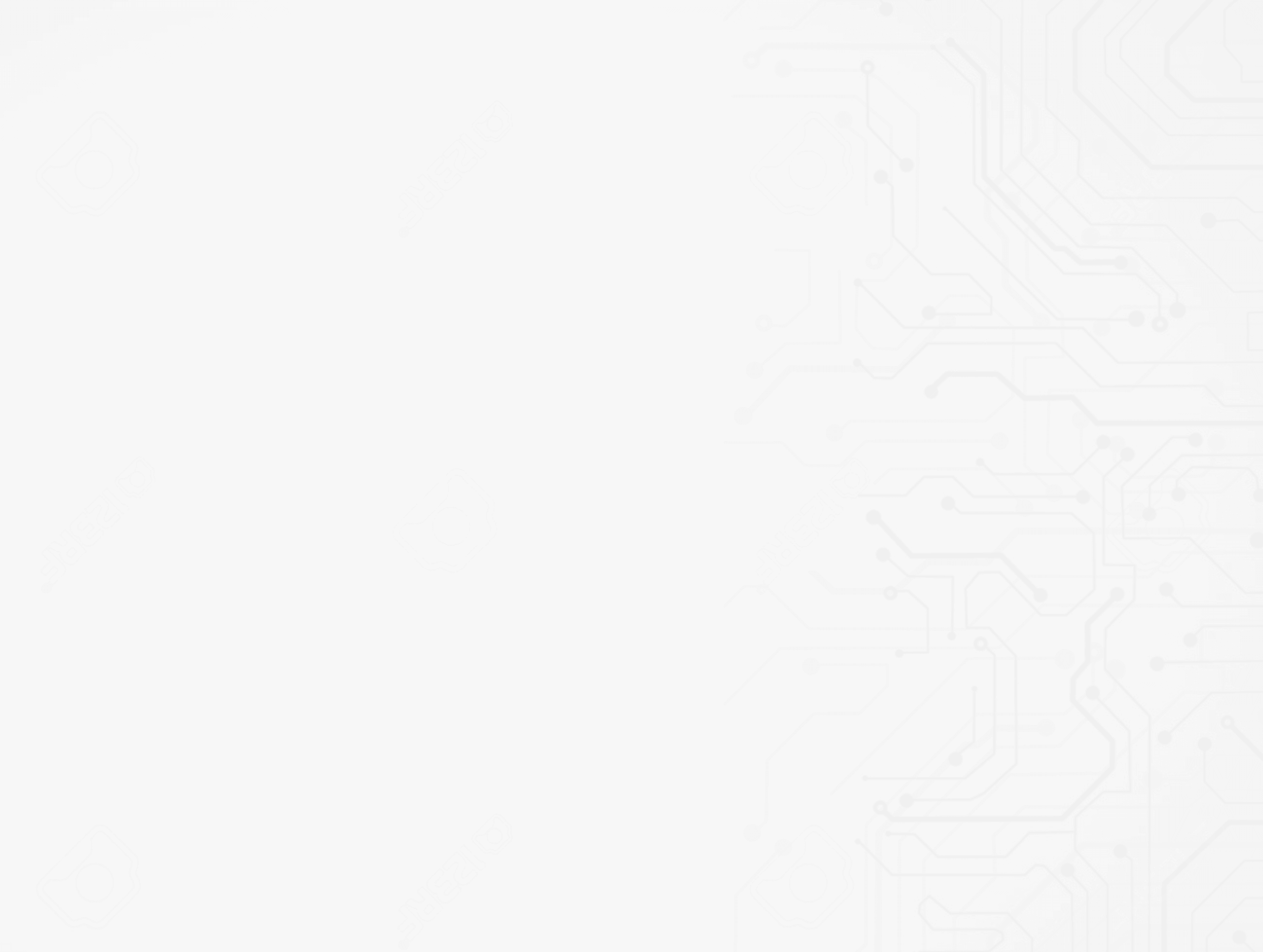
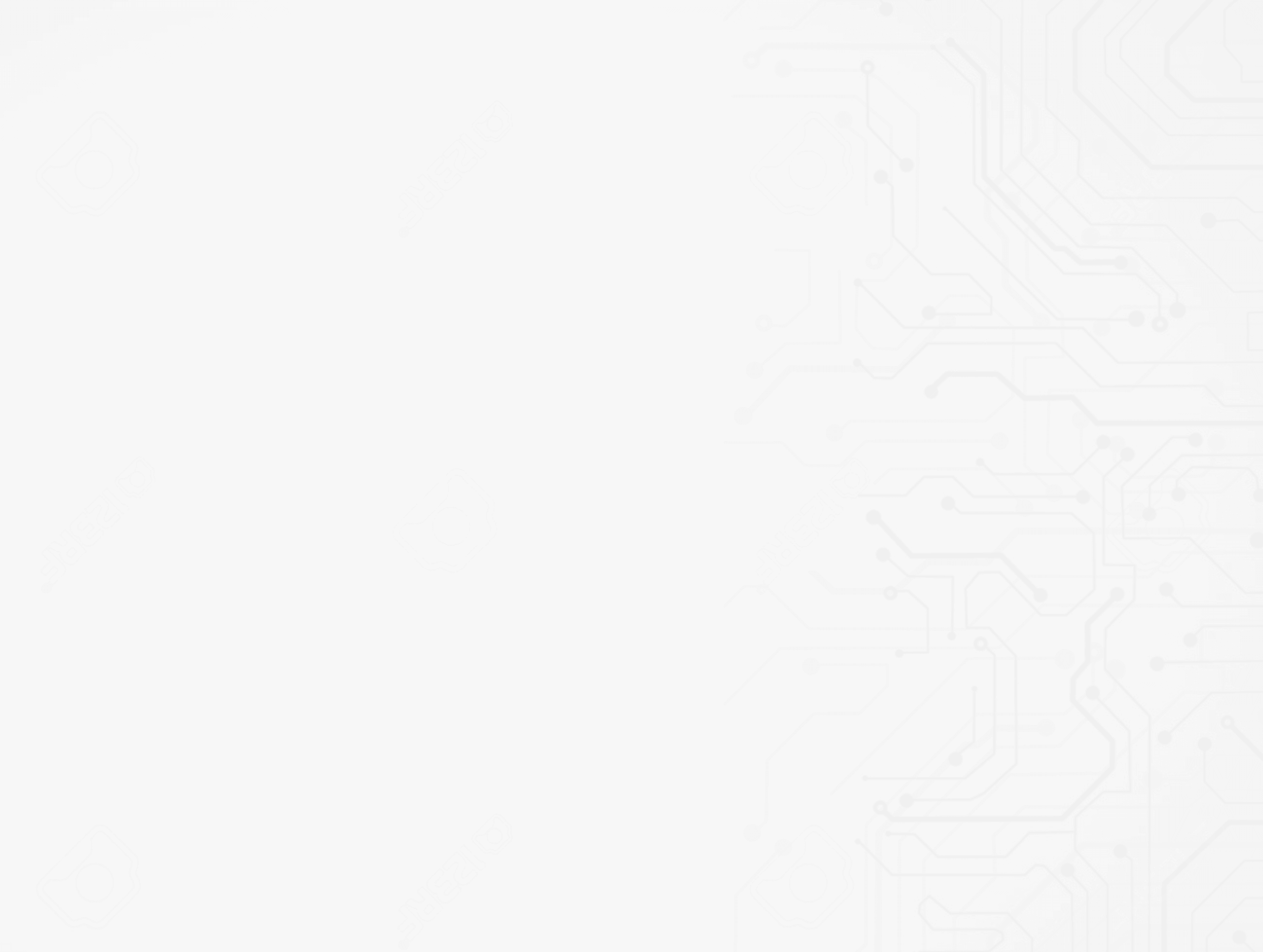
—— Inspection equipment ——
Features:
1. Burr measurement.
2. 2.Product bending angle (inner R) measurement → Determine whether the mold design is appropriate.
3. Size measurement.
1. Burr measurement.
2. 2.Product bending angle (inner R) measurement → Determine whether the mold design is appropriate.
3. Size measurement.
Size inspection for width and thickness
Professional inspection machine
Able to confirm the material quality (preliminarily ensuring the material properties) including material appearance, width, flatness, bending, and burrs before cutting the masterbatch.

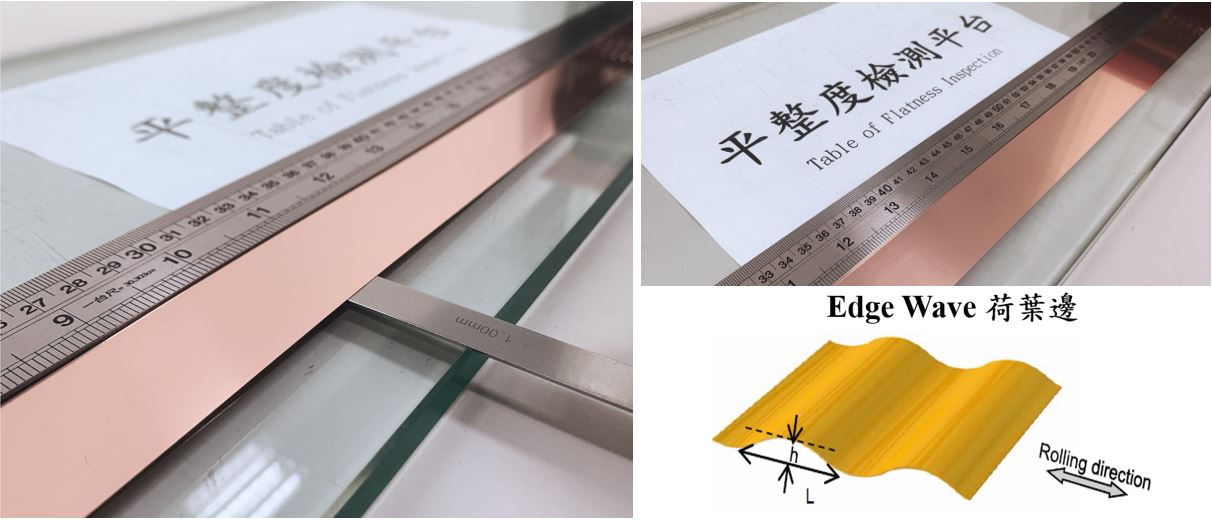
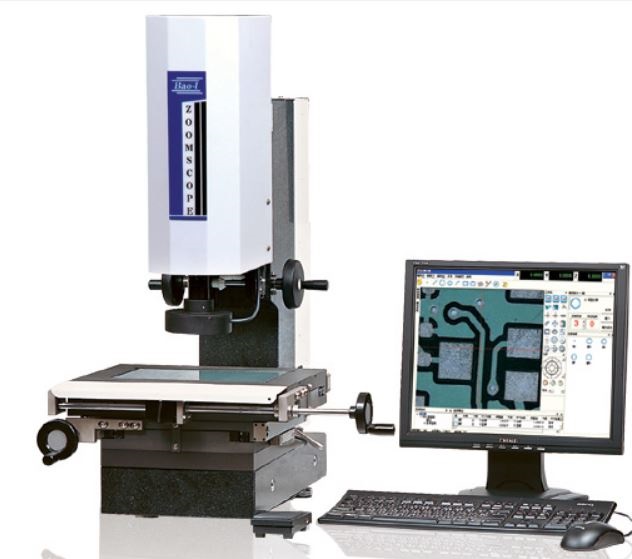
2.5D image measuring instrument

Burr inspection
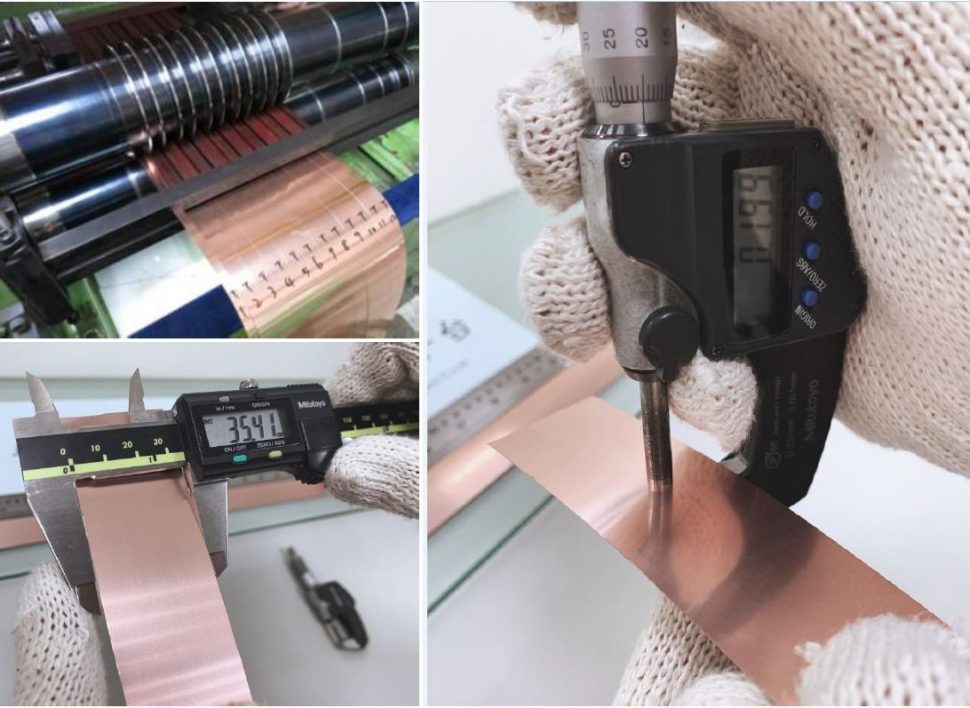
Warpage inspection platform
Flatness inspection
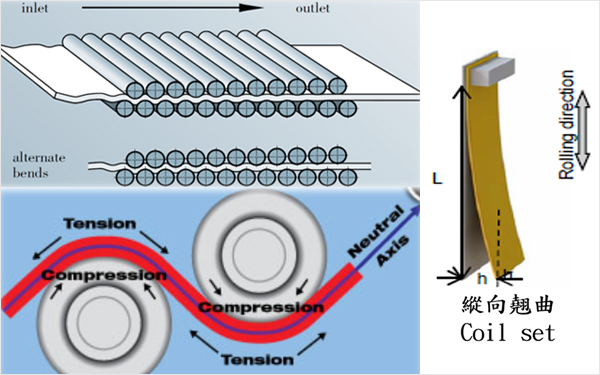
Warpage inspection
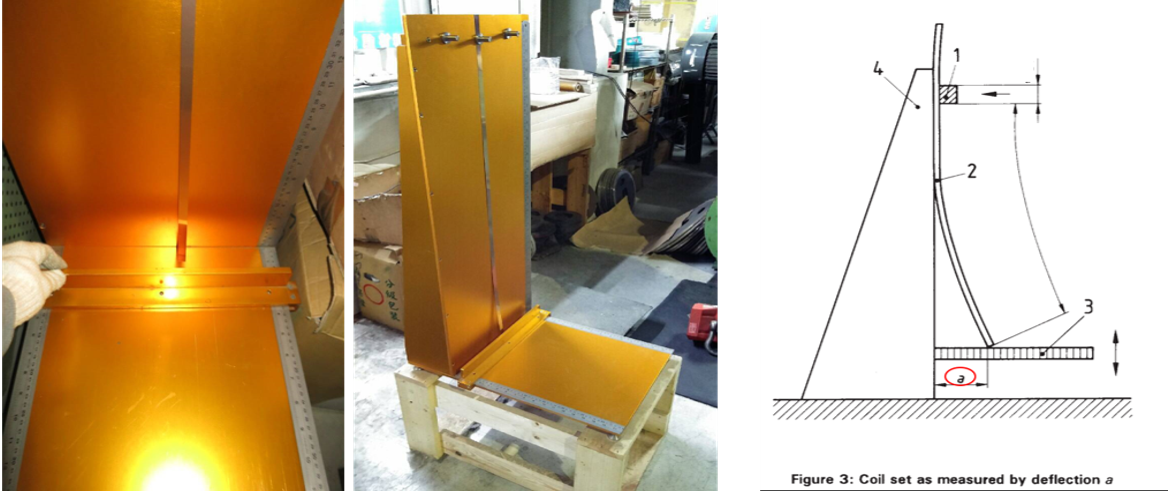
International standards: Not exceeding 80mm/1 meter (i.e. the a of 1-meter sample < 80mm).
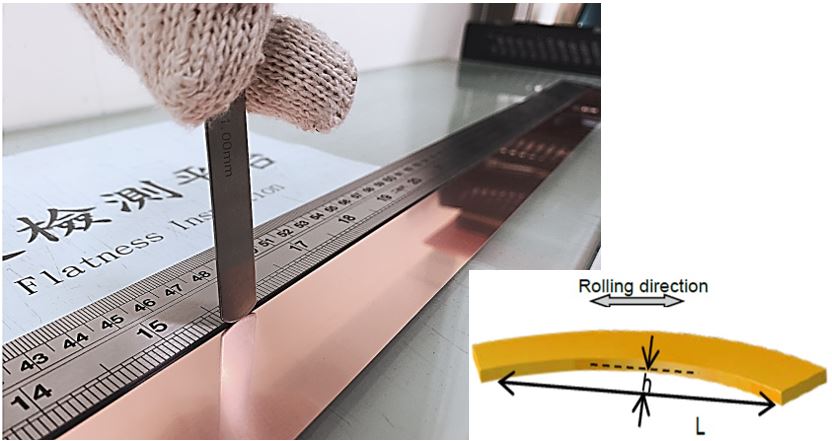
Curvature inspection

Versatile tensile testing machine
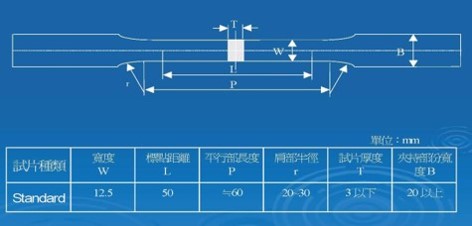
Versatile tensile testing machine - Test sample
a. The material size conforms to the international standards or not b. The existence of burrs on test sample c. The test sample is clamped firmly or not;
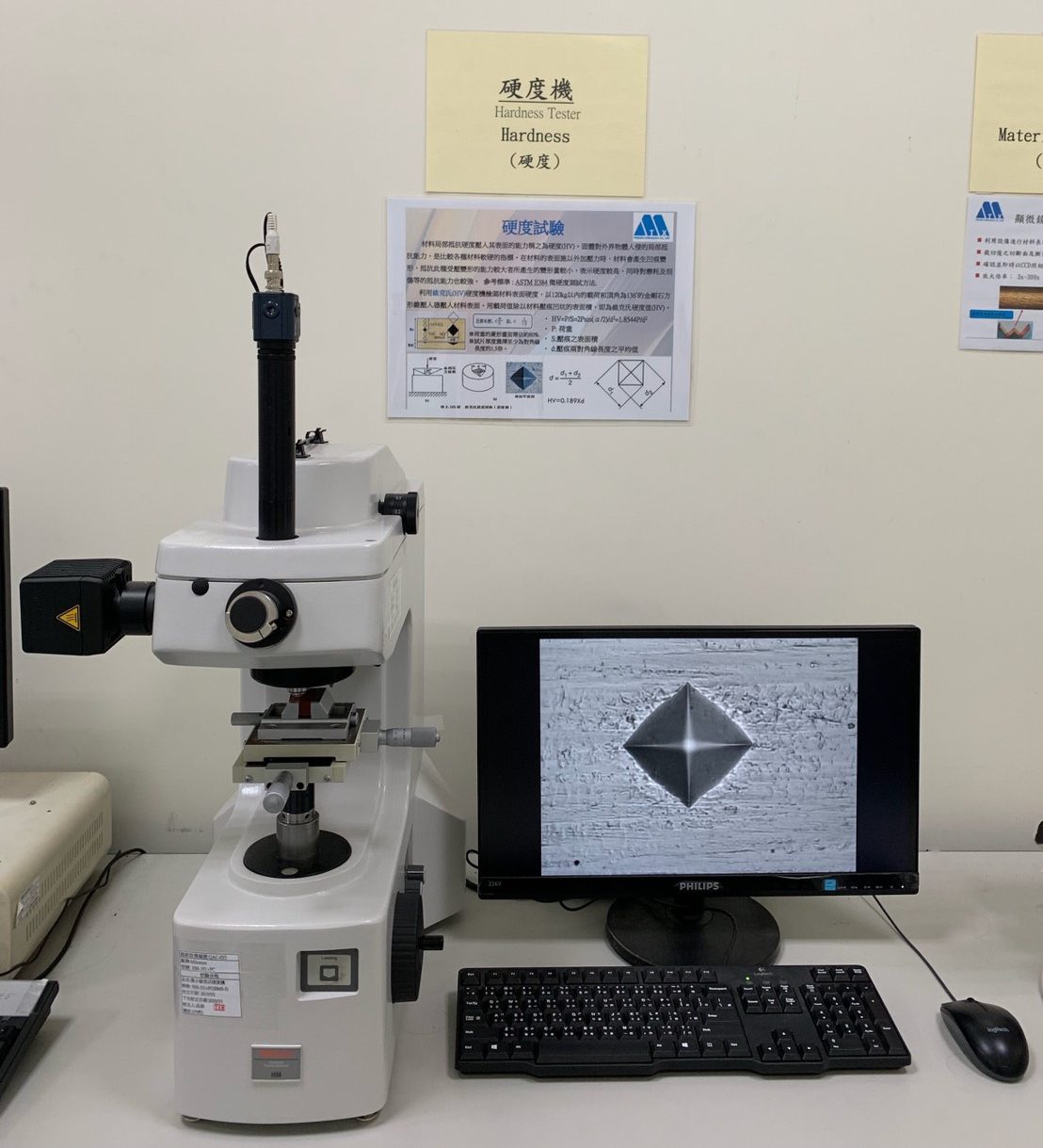
B.Appropriateness of the pressing load.
C.Symmetry of cross symmetry line.
90-degree bending test

Manual stamping machine (90-degree bending test)

Hardness testing machine

High-magnification microscopes
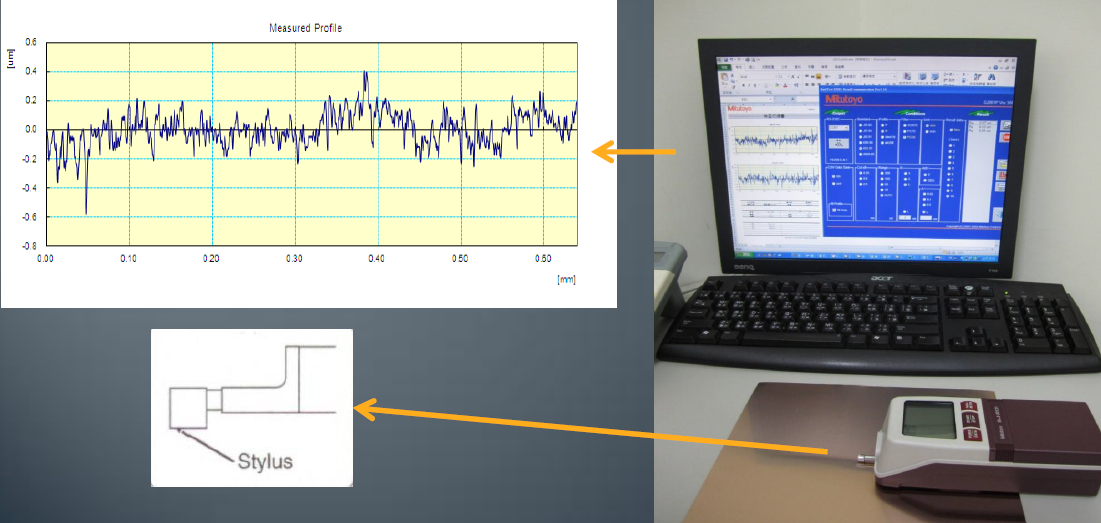
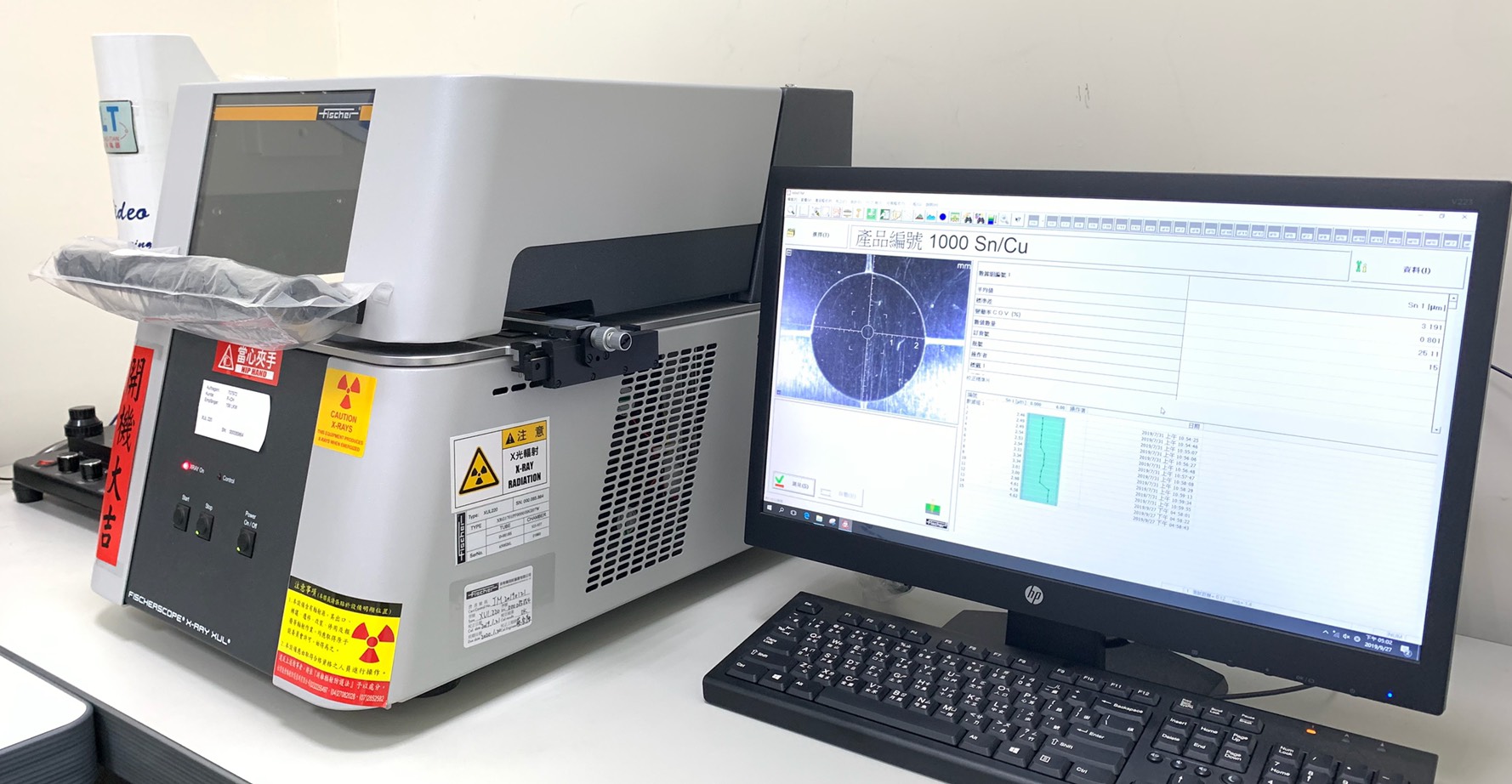
